Capsules are a significant part of the oral solid dosage (OSD) forms, widely used in pharmaceutical therapies. Despite their extensive use and established manufacturing lineage, capsules can pose considerable challenges. With the rise in complex molecules, it is crucial to offer diverse formulation and oral solid solutions for capsules.
Regardless of your project’s size or stage, we embrace your challenges and possess the expertise to deliver a broad range of capsule forms. This includes:
- Hard and soft gelatin capsules
- Delayed and extended-release capsules
- Capsules for liquid, semi-solid, and solid fills
- Capsules for dry powder inhalation (DPI)
- Enteric-coated capsules
- Capsules with beadlets or pellets for modified release
- Capsules for reconstitution
- Capsules with multiple-particulate fluid bead coating
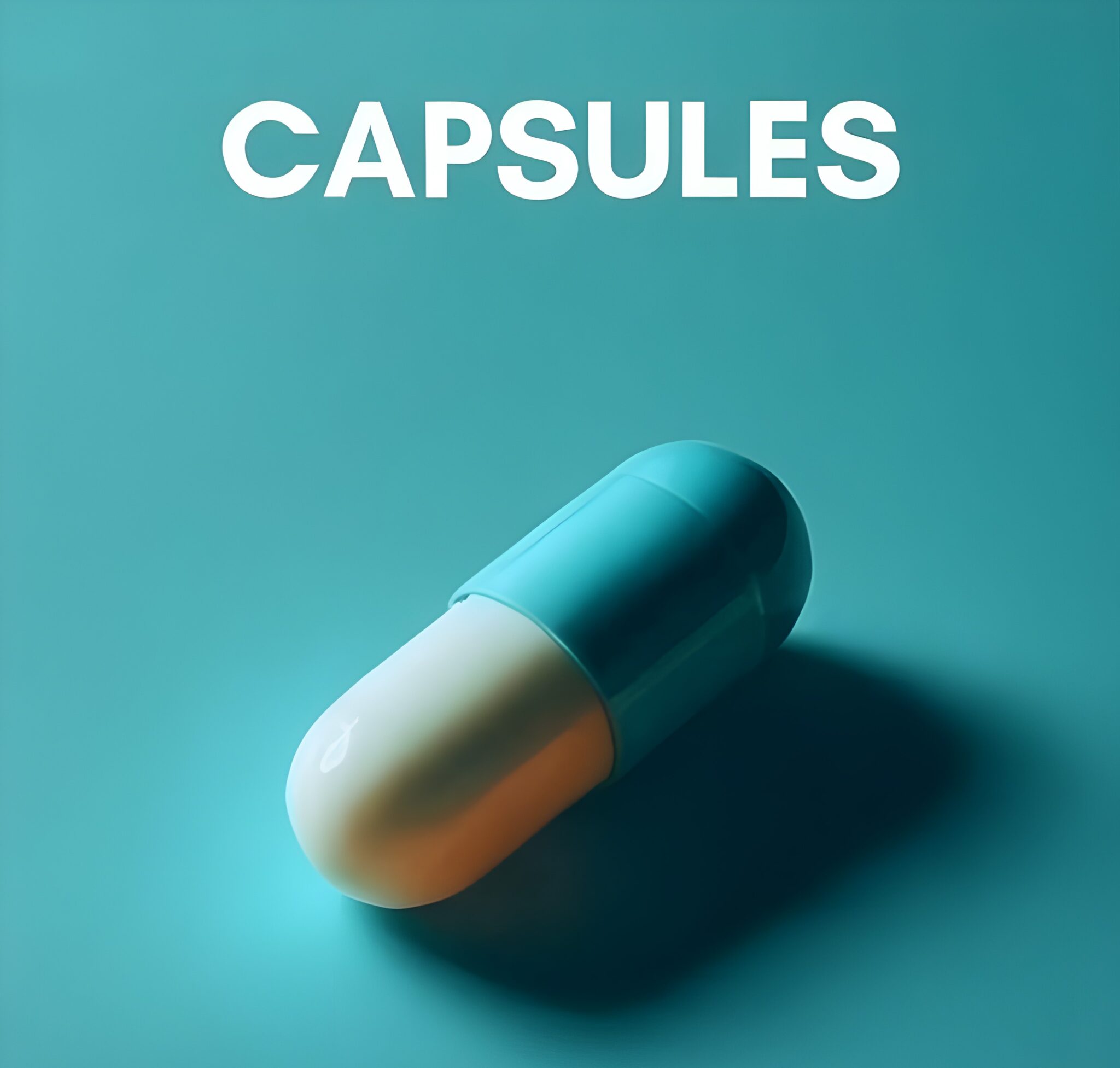
Capsule Forms Offered
At Hycon Labs, we offer a comprehensive range of services in capsule manufacturing, tailored to meet diverse therapeutic needs and patient preferences. Our extensive expertise encompasses various types of capsules, each meticulously designed to address specific clinical requirements and enhance patient compliance. Here’s an in-depth look at the array of capsule forms we provide:
Hard Gelatin Capsules
Our specialization in the production of hard gelatin capsules stands out in the pharmaceutical industry. These capsules, comprising two distinct pieces, are particularly suitable for encapsulating dry powder formulations. Their robust design ensures excellent stability and an extended shelf life, making them ideal for a multitude of pharmaceutical applications. Hard gelatin capsules provide a versatile and reliable delivery system for a wide range of active pharmaceutical ingredients (APIs), ensuring the efficacy and longevity of the medication.
Soft Gelatin Capsules
Soft gelatin capsules are another key offering in our portfolio, designed to encapsulate liquid or semi-solid fills. These capsules are especially beneficial for oil-based formulations, significantly enhancing the bioavailability of poorly soluble drugs. The seamless, single-piece construction of soft gelatin capsules allows for precise dosing and protects the contents from oxidation and degradation. This form of encapsulation is particularly advantageous for delivering fat-soluble vitamins, essential oils, and other lipophilic compounds.
Modified Release Capsules
Our modified release capsules are engineered to alter the drug release rate, aiming to achieve a sustained therapeutic effect or to optimize drug delivery. We offer several variations, including sustained-release, controlled-release, and delayed-release capsules. These advanced formulations are designed to release the active ingredient at a predetermined rate, providing consistent drug levels over an extended period. This approach minimizes the frequency of dosing, enhances patient adherence to treatment regimens, and reduces potential side effects associated with peak drug concentrations.
Enteric-Coated Capsules
Enteric-coated capsules are designed with a special coating that resists the acidic environment of the stomach and dissolves in the more alkaline environment of the intestine. This technology is particularly beneficial for drugs that are either destroyed by stomach acid or can cause irritation to the stomach lining. By ensuring the active ingredient is released only in the intestine, enteric-coated capsules enhance the therapeutic efficacy and safety profile of the medication. This form of delivery is crucial for drugs like proton pump inhibitors, certain antibiotics, and other acid-sensitive compounds.
Custom Formulations
Recognizing that each drug possesses unique formulation needs, our team of expert pharmacists and scientists excels in developing custom capsule formulations tailored to your specific requirements. Whether you need a unique combination of APIs, specific release profiles, or particular excipient selections, we have the expertise and flexibility to create formulations that meet your precise specifications. Our collaborative approach ensures that we deliver solutions that align perfectly with your therapeutic goals and market demands.
Quality Assurance and Control
Quality is the cornerstone of our manufacturing process. We adhere to stringent quality control measures at every stage of production to ensure the safety, efficacy, and consistency of our capsules. Our state-of-the-art facilities are equipped with advanced analytical instrumentation, and our quality assurance team rigorously monitors each batch to meet the highest standards of pharmaceutical manufacturing. From raw material sourcing to final product inspection, our commitment to quality ensures that our capsules perform reliably and meet all regulatory requirements.
Regulatory Support
Navigating the complex landscape of regulatory compliance is a critical aspect of pharmaceutical manufacturing. We provide comprehensive regulatory support to ensure that our capsules meet all necessary compliance requirements. Our dedicated regulatory affairs team stays abreast of the latest regulatory changes and offers assistance with documentation, submissions, and audits. This proactive approach helps streamline the approval process, reduces time-to-market, and ensures that your products adhere to global regulatory standards.
At Hycon Labs, we are committed to delivering high-quality capsule manufacturing services that meet the needs of our clients and contribute to improved patient outcomes. Our unwavering focus on innovation, quality, and regulatory compliance positions us as a trusted partner in the pharmaceutical industry, dedicated to advancing healthcare through superior capsule formulations.
Capsules Manufacturing Process
Formulation Development
The process of formulation development begins with the careful selection and preparation of the active pharmaceutical ingredient (API). This stage is crucial because the API is the primary component that provides the therapeutic effect of the medication. Scientists and researchers must consider various factors when choosing the API, including its chemical stability, solubility, and bioavailability. Additionally, the choice of excipients, which are inactive substances used as carriers for the API, is equally important. Excipients can include binders, fillers, disintegrants, lubricants, and coatings, each serving a specific purpose to ensure the stability, efficacy, and patient acceptability of the final product. Preservatives are also added to prevent microbial growth, and stabilizers are used to maintain the physical and chemical integrity of the formulation over its shelf life. The selection process is meticulous and involves extensive research, testing, and validation to ensure that the final formulation meets all regulatory requirements and delivers the intended therapeutic benefits to patients.
Mixing and Homogenization
Once the formulation is developed, the next critical step is the mixing and homogenization of the API and excipients. This process ensures that the active ingredient is evenly distributed throughout the mixture, providing consistent dosing in each capsule. Advanced mixing equipment is used to achieve a uniform blend, which is essential for the quality and efficacy of the final product. Homogenization involves breaking down particles to create a uniform mixture, which can be particularly important for formulations where particle size affects the drug’s bioavailability and absorption. The equipment used in this stage is often highly sophisticated, capable of precise control over mixing parameters to achieve the desired consistency and homogeneity.
Capsule Filling
The filling of capsules is a highly automated process, utilizing state-of-the-art filling machines to ensure accuracy and efficiency. These machines are designed to handle large volumes of capsules, making the process cost-effective, especially when partnering with a Contract Development and Manufacturing Organization (CDMO). This partnership allows pharmaceutical companies to leverage the CDMO’s expertise and infrastructure, reducing the overall investment required for manufacturing. For soft gelatin capsules, the filling process is unique; it involves a single rotary die encapsulation machine that simultaneously forms, fills, and seals the capsules. This method ensures that the capsules are airtight and properly sealed, protecting the contents from environmental factors that could compromise their stability and efficacy.
Quality Control
Quality control is a fundamental aspect of pharmaceutical manufacturing, ensuring that each batch of capsules meets stringent specifications for potency, purity, and dissolution. This involves a series of rigorous tests conducted throughout the manufacturing process, from raw material inspection to final product evaluation. Analytical techniques such as high-performance liquid chromatography (HPLC), gas chromatography (GC), and mass spectrometry (MS) are commonly used to verify the chemical composition and concentration of the API and excipients. Additionally, dissolution testing is performed to ensure that the capsules will release the active ingredient at the correct rate and extent in the body. Any batch that fails to meet the predefined criteria is rejected and investigated to identify and rectify the cause of the discrepancy.
Packaging
The packaging of capsules is a critical step to protect the product from physical damage, contamination, and degradation due to environmental factors such as light, moisture, and temperature. Packaging materials are carefully selected based on the specific requirements of the medication, with common options including blister packs, bottles, and pouches. Each type of packaging is designed to provide a barrier against external elements, ensuring that the capsules remain stable and effective throughout their shelf life. Additionally, packaging often includes tamper-evident features to enhance security and patient safety.
Printing
To ensure proper identification and traceability, capsules can be printed with unique markings. These markings can include the drug name, dosage, manufacturer logo, or other identifying codes. The printing process uses advanced technology to apply precise and durable ink to the capsule surface, ensuring that the markings remain legible throughout the product’s use. This step not only helps in preventing medication errors but also aids in compliance with regulatory requirements for pharmaceutical products.
Testing, Packaging, and Shipping
The final stage of the manufacturing process involves additional testing, packaging, and shipping. After the initial quality control checks, each batch undergoes further testing to confirm that it meets all specifications for potency, purity, and dissolution. Once approved, the capsules are packaged in their final containers, ready for distribution. Packaging methods are designed to protect the capsules during transportation, ensuring they arrive at their destination in optimal condition. The logistics of shipping are carefully planned to maintain the integrity of the product, considering factors such as temperature control and handling procedures. This comprehensive approach ensures that the medication reaches patients in the best possible condition, ready to provide the intended therapeutic effects.
Additional Benefits
Capsules offer several significant advantages in the realm of oral medication delivery, which make them a preferred choice for many patients and healthcare providers. Each of these benefits contributes to the overall effectiveness and user experience of the medication.
Easy to Swallow: Capsules are often designed with a smooth, gelatinous exterior that can make them easier to swallow compared to other oral dosage forms such as tablets or hard pills. The streamlined shape and coating of capsules reduce the likelihood of causing discomfort or gagging, making them particularly advantageous for individuals who experience difficulty with traditional pill forms. This is especially important for populations such as elderly patients, children, or those with certain medical conditions that impair swallowing.
Tasteless and Odorless: One of the distinct advantages of capsules is their ability to mask the taste and odor of the medication inside. The outer shell of a capsule, typically made from gelatin or a similar material, encases the drug in a way that prevents its flavor or smell from being detected by the taste buds or olfactory senses. This feature is especially valuable for medications that have a naturally unpleasant taste or odor, thereby improving patient compliance by making the medication experience more palatable.
Rapid Dissolution: Capsules generally exhibit a faster dissolution rate compared to tablets. This rapid breakdown can facilitate quicker disintegration of the drug in the gastrointestinal tract, which may lead to faster onset of therapeutic effects. The gelatin or other materials used in the capsule shell dissolve more readily when exposed to stomach acids, allowing for the medication inside to be released and absorbed into the bloodstream more promptly.
Tamper-Resistant: Capsules are often engineered with tamper-resistant features that enhance their security and integrity. Unlike tablets, which can be split or crushed to alter their dosage, capsules are designed in a way that makes it difficult to divide them without compromising their effectiveness or safety. This feature helps prevent misuse or accidental overdose and ensures that the medication is administered in its intended form, maintaining its efficacy and reducing the risk of contamination.
Versatility: The versatility of capsules is a key benefit, as they can accommodate a wide variety of medication forms, including powders, granules, pellets, or even liquids. This flexibility allows pharmaceutical companies to formulate medications in a manner that optimizes their stability, delivery, and absorption. For example, capsules can be used to encapsulate ingredients that might not be suitable for compression into a tablet form or to combine multiple active ingredients into a single dose.
Controlled Release: Certain specialized capsules are designed to provide controlled or extended release of their contents. These capsules can be formulated to gradually release the medication over an extended period, thereby ensuring a sustained therapeutic effect. This controlled-release mechanism helps maintain consistent drug levels in the bloodstream, potentially reducing the frequency of dosing and improving overall treatment outcomes by minimizing fluctuations in drug concentration.
Improved Bioavailability: Capsules can sometimes enhance the bioavailability of certain drugs, which refers to the proportion of the drug that enters the bloodstream and is available for therapeutic action. The design of the capsule and the choice of excipients can influence the drug’s solubility and absorption. By improving the dissolution and absorption characteristics of the medication, capsules can increase the overall effectiveness of the drug and ensure that it reaches its target site more efficiently.
Patient Adherence: The user-friendly nature of capsules, including their ease of swallowing, tastelessness, and quick dissolution, contributes to improved patient adherence to medication regimens. When patients find their medication regimen to be convenient and comfortable, they are more likely to follow it consistently. This adherence is crucial for achieving desired therapeutic outcomes and managing chronic conditions effectively, ultimately leading to better health outcomes and enhanced quality of life.
Overall, the diverse benefits of capsules, from their ease of use and versatility to their potential for controlled release and improved bioavailability, make them a valuable dosage form in modern pharmacotherapy.
Services
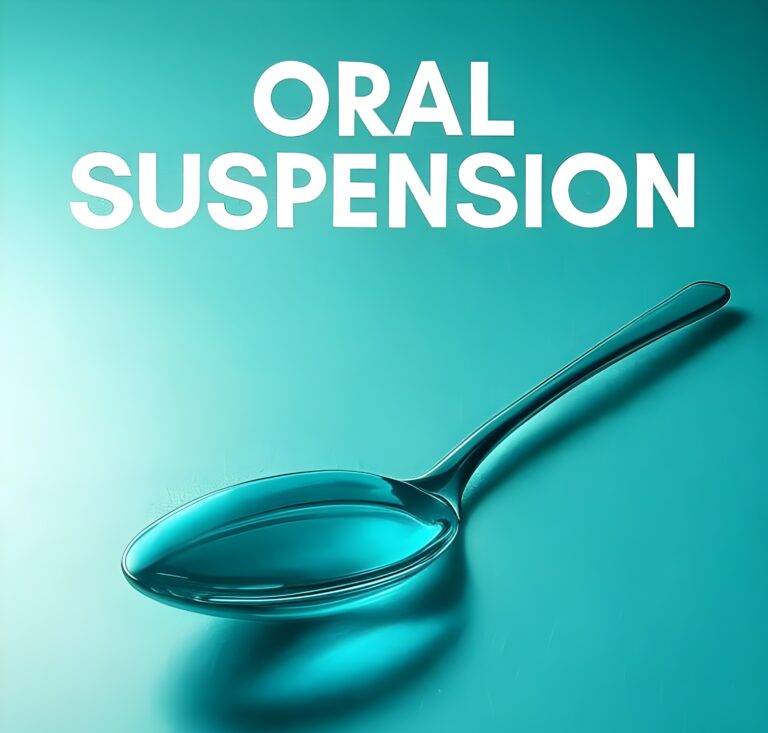
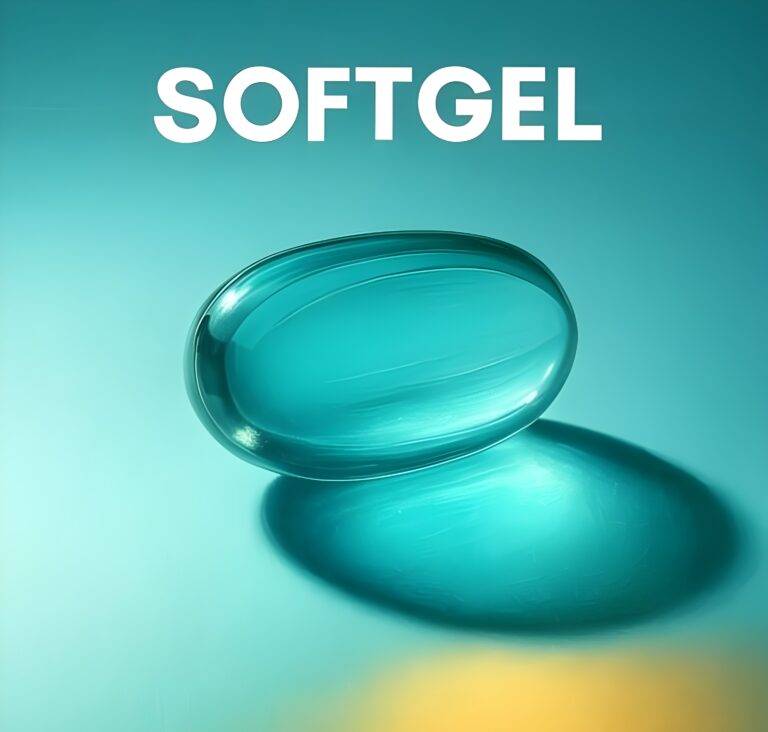
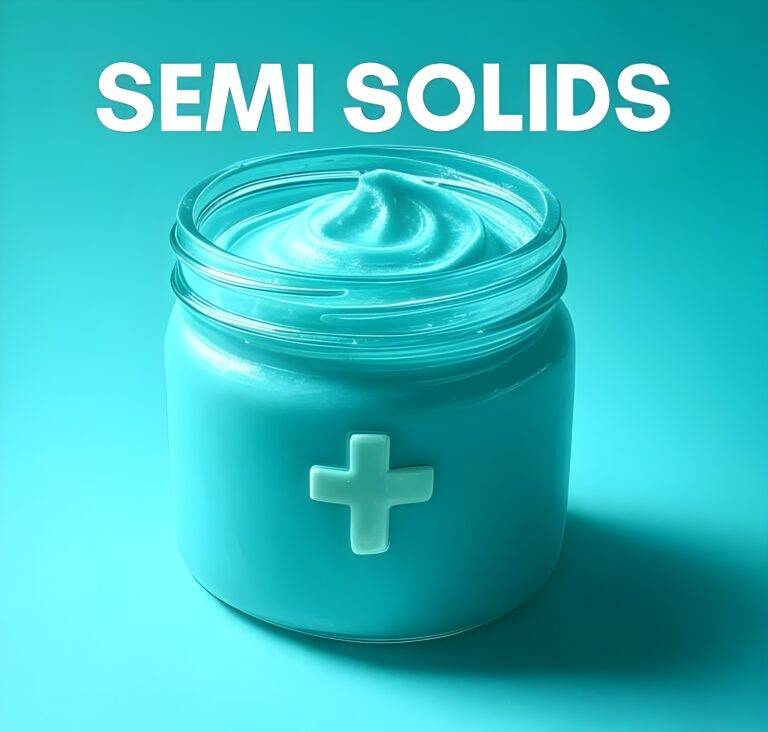
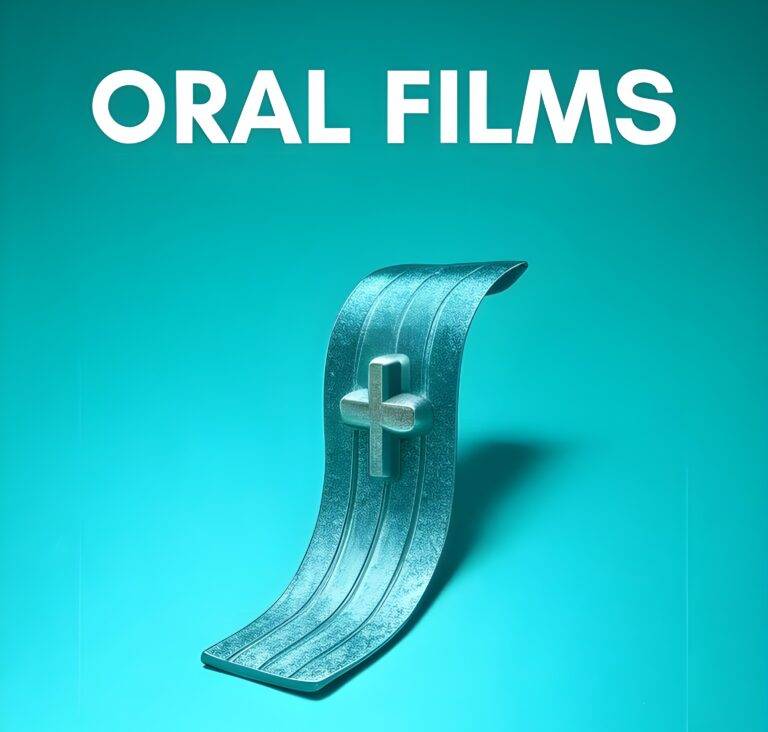
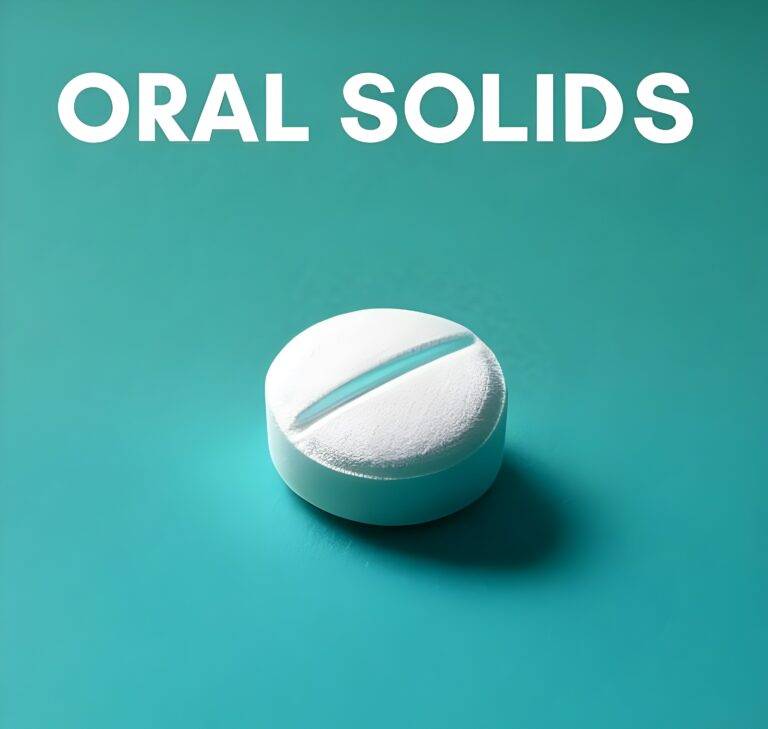
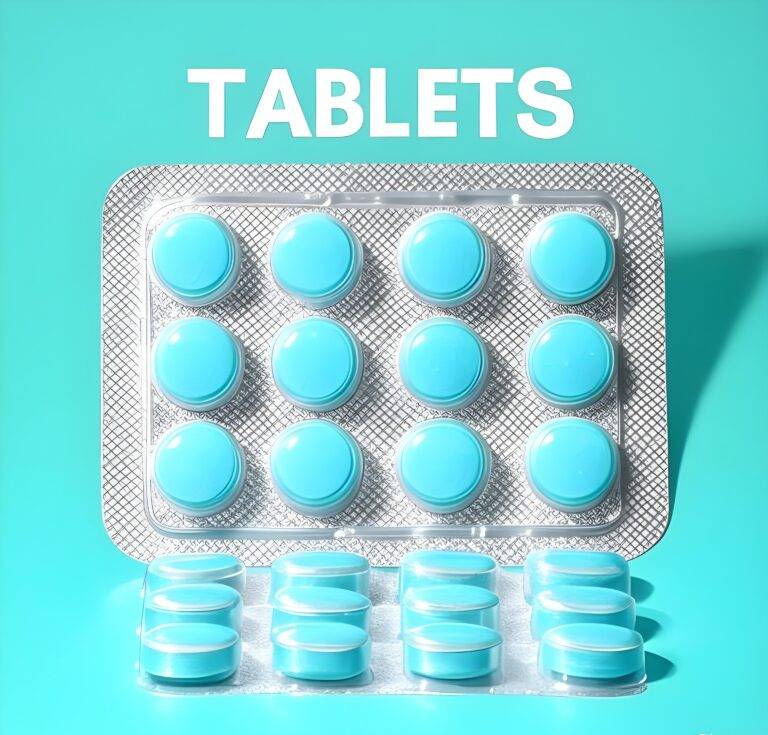
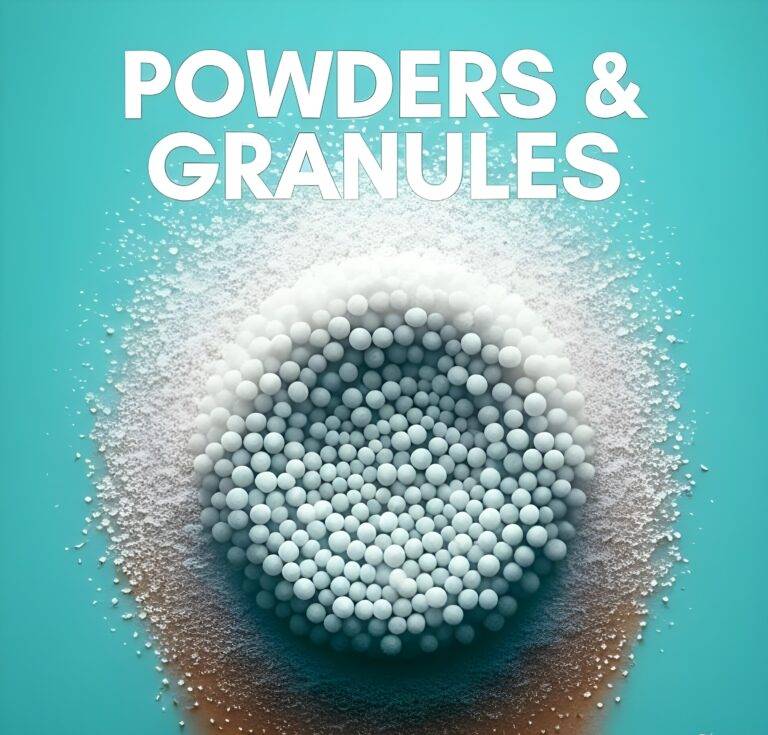
FAQs
Here are some frequently asked questions about Oral Solids
Oral solid dosage forms include tablets, capsules, powders, and granules. They are the most popular method of drug delivery due to their convenience, stability, and ease of mass production. These forms allow for precise dosages, extended shelf life, and improved patient compliance, making them a staple in both over-the-counter and prescription medication markets.
We offer comprehensive services for oral solid dosage forms, including formulation development, process optimization, scale-up, and manufacturing. Our capabilities extend to immediate and controlled-release formulations, coating, encapsulation, and the development of chewable, dispersible, and effervescent tablets. We also provide packaging and analytical testing services to ensure product quality and compliance.
Quality and compliance are paramount in our operations. We adhere to Good Manufacturing Practices (GMP) and are regularly inspected by regulatory authorities like the FDA and EMA. Our quality control processes include rigorous testing of raw materials, in-process materials, and finished products. We also implement robust quality assurance protocols, including validation and stability studies, to ensure our products meet all regulatory standards.
Yes, we have specialized facilities and containment systems designed to safely handle controlled substances. Our team is experienced in managing the unique challenges associated with these substances, including stringent regulatory requirements and the need for specialized equipment and safety protocols.
Our production capacity is flexible and scalable to meet the needs of our clients, ranging from small-scale batch production for clinical trials to large-scale manufacturing for commercial supply. Our facilities are equipped with state-of-the-art machinery for granulation, compression, and coating, allowing us to efficiently produce a wide range of batch sizes with high precision and consistency.
For generic products, we focus on bioequivalence studies, cost-effective formulation, and process optimization to ensure competitive market entry. For novel oral solid dosage forms, we collaborate closely with our clients to develop innovative formulations that enhance bioavailability, improve patient compliance, and extend product lifecycle, leveraging our expertise in drug delivery technologies and formulation science.
Our formulation development and optimization process is data-driven and collaborative. We utilize Quality by Design (QbD) principles, incorporating thorough understanding of the drug substance, target product profile, and manufacturing processes. We employ advanced modeling and simulation tools, along with high-throughput screening methods, to rapidly identify and optimize formulations that meet the desired product attributes.
Project management is a core competency of our operations. We assign dedicated project managers to each client, who oversee all aspects of the project from inception to delivery. Our project managers work closely with clients to establish clear timelines, milestones, and communication plans. We utilize agile manufacturing practices and real-time monitoring to ensure projects remain on track and adjustments are made proactively to meet delivery commitments.
While confidentiality agreements restrict the details we can share, we have successfully partnered with numerous pharmaceutical companies to bring both generic and innovative oral solid dosage products to market. Our collaborations often involve overcoming complex formulation challenges, scaling up novel production processes, and navigating regulatory approvals efficiently.
Starting a project with us is straightforward. Interested pharmaceutical companies can contact us through our website, email, or phone to schedule an initial consultation. During this consultation, we discuss the project scope, objectives, and timelines. Following this, we provide a proposal outlining our services, timelines, and cost estimates. Upon agreement, we initiate the project with a kick-off meeting to align on project details and establish communication protocols.