We offer a comprehensive suite of solutions that address the challenges of drug solubility and efficacy. Our advanced techniques in particle size engineering are crucial for optimizing the bioavailability and therapeutic performance of active pharmaceutical ingredients (APIs).
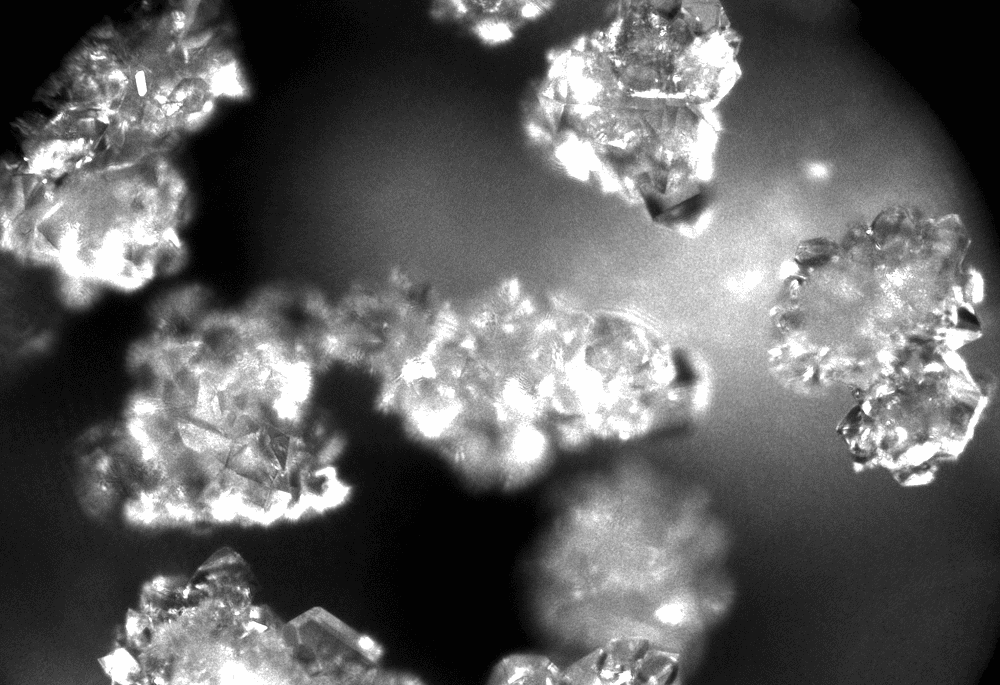
Micronization And Nano-Milling
Our employees have decades of jet milling experience with hundreds of compounds which have enabled capabilities and expertise in micronization and particle classification.
ASD via Hot Melt and Spray Drying
Our centers of excellence for solid dispersions in Happaugue and Central Islip (US) offer integrated product design, development and manufacturing of intermediates based on SDD, hot melt extrusion and others.
Avoid a Tech Transfer
As part of our integrated product development services, we offer scalable particle engineering capabilities from early stage design through to scale-up and commercialization.
Phase Appropriate Services
We provide phase appropriate particle-engineering services, a customized and fit-for-purpose particle engineering service as part of our integrated drug substance and drug product offering. You can access:
- Spray dryers
- Hot-melt extrusion
- Melt-spray congealing
- Phase-appropriate particle size reduction processing
- End to end milling
Each offering is in place to help advance your compound from concept to clinical and commercialization.
Particle size reduction to precise particle size distribution is in place for API milling across pin mill, hammer mill, jet mill and nano-mill processing at our NY sites, Our particle engineering services using spray drying, hot-melt extrusion, or melt-spray-congealing.
Particle Size Reduction
Particle size reduction is an important material engineering to improve bioavailability and achieve certain specifications . The micronization and/or milling process generates a more consistent particle size distribution, thereby enhancing pharmaceutical formulations. To satisfy cGMP guidelines and deliver results, scientists must seek particle size reduction services that use specialized equipment, while offering support for customized protocol development, validation, execution and reporting.
Effective particle size reduction requires an understanding of many material characteristics, including particle size distribution, hardness and flowabilty. Formulations may also require specialized protocols based on the potency of the active ingredients. Hycon works to understand the requirements of your formulations, with robust particle size testing and analyses. This knowledge is then passed to you as part of a final project report.
Small Molecules Particle Engineering Services
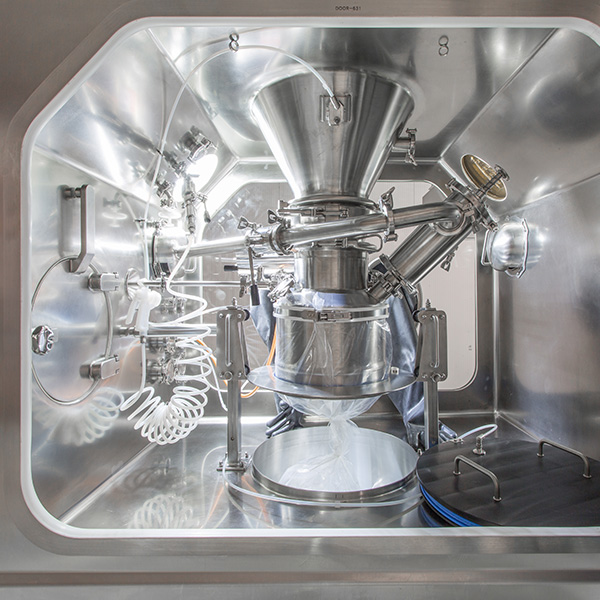
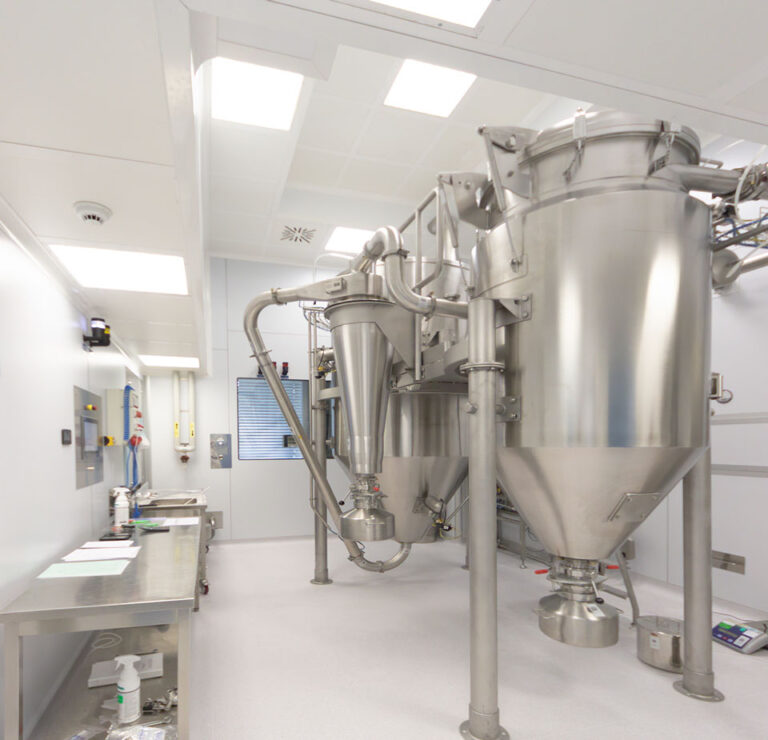
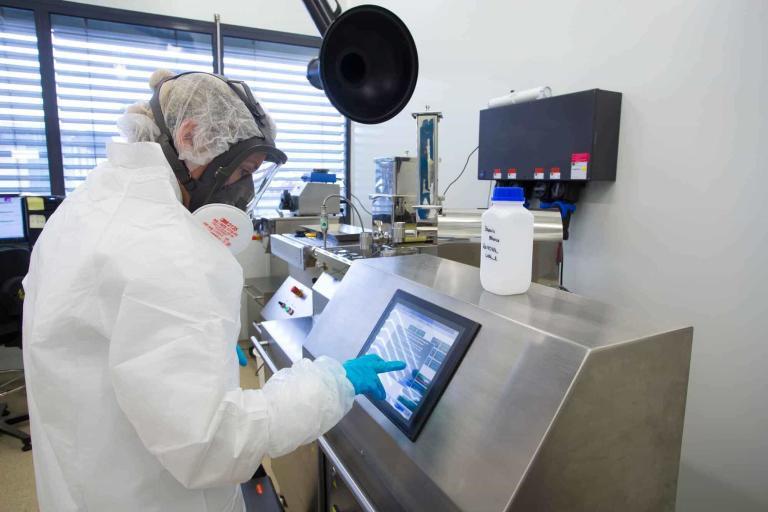
FAQs
Here are some frequently asked questions about Particle Engineering
Particle engineering is a branch of pharmaceutical development that focuses on modifying the size, shape, structure, and surface properties of particles to improve their performance in drug formulations. This process is crucial for enhancing solubility, bioavailability, stability, and manufacturability of pharmaceuticals. Particle engineering techniques can be applied to a wide range of materials, including active pharmaceutical ingredients (APIs), excipients, and final drug products.
Particle engineering is important in pharmaceutical development because the physical and chemical properties of particles can significantly affect the efficacy, safety, and patient compliance of drug products. Optimizing particle characteristics can enhance drug solubility and dissolution rates, improve drug delivery to specific sites within the body, reduce dosage frequency, and minimize side effects. It also allows for the development of novel drug delivery systems and the extension of patent life for existing drugs.
Common techniques used in particle engineering include milling (such as jet milling and ball milling), high-pressure homogenization, spray drying, freeze drying, crystallization, and supercritical fluid technology. Each technique has its advantages and is selected based on the desired outcome for the particle's properties, the nature of the drug substance, and the intended application of the final product.
Particle engineering can improve drug solubility and bioavailability by reducing the particle size (nanonization), altering the crystal form to a more soluble polymorph or amorphous state, and engineering the particle surface to enhance dissolution. These modifications increase the surface area of the drug, improving its interaction with solvents and facilitating faster and more complete absorption into the bloodstream.
A CDMO provides comprehensive particle engineering services, from initial concept and feasibility studies to scale-up and commercial manufacturing. Services include selecting the appropriate engineering technique, optimizing process parameters, conducting material characterization studies, and ensuring that the engineered particles meet the required specifications for clinical efficacy and regulatory compliance. A CDMO also offers expertise in formulation development and analytical testing to support the successful integration of engineered particles into drug products.
Particle engineering can be applied to a broad range of drugs, including small molecule drugs, biologics, and poorly soluble compounds. However, the specific techniques and approaches used may vary depending on the chemical and physical properties of the drug, its intended route of administration, and the target drug delivery profile. A CDMO can provide guidance on the feasibility and best practices for particle engineering for each specific drug type.
Challenges in particle engineering include achieving the desired particle size distribution, maintaining particle stability during processing and storage, controlling the polymorphic form of crystalline materials, and ensuring reproducibility and scalability of the engineering process. Addressing these challenges requires a deep understanding of material science, pharmaceutical formulation, and the specific engineering techniques employed.
Particle engineering can impact the regulatory approval process by necessitating thorough characterization and validation of the engineered particles and the processes used to produce them. Regulatory agencies require detailed information on particle size distribution, polymorphism, solubility, and bioavailability, as well as stability data and manufacturing controls. A CDMO with experience in regulatory submissions can help navigate these requirements, ensuring that particle engineering efforts contribute positively to the drug's regulatory pathway.
Quality control measures in particle engineering include rigorous testing of particle size and size distribution, crystal form, purity, and surface characteristics. In-process controls are also critical for monitoring and adjusting parameters to maintain consistent production quality. Adherence to Good Manufacturing Practices (GMP) and implementation of robust analytical methods are essential for ensuring the quality of engineered particles.
Choosing the right particle engineering technique involves considering several factors, including the physical and chemical properties of the drug substance, the desired modifications to the particles, the scalability of the process, and the cost-effectiveness of the technique. Compatibility with the final drug formulation and the intended route of administration are also critical considerations. A CDMO with expertise in particle engineering can provide valuable insight and guidance in selecting the most appropriate technique for each project, based on comprehensive feasibility studies and development experience.