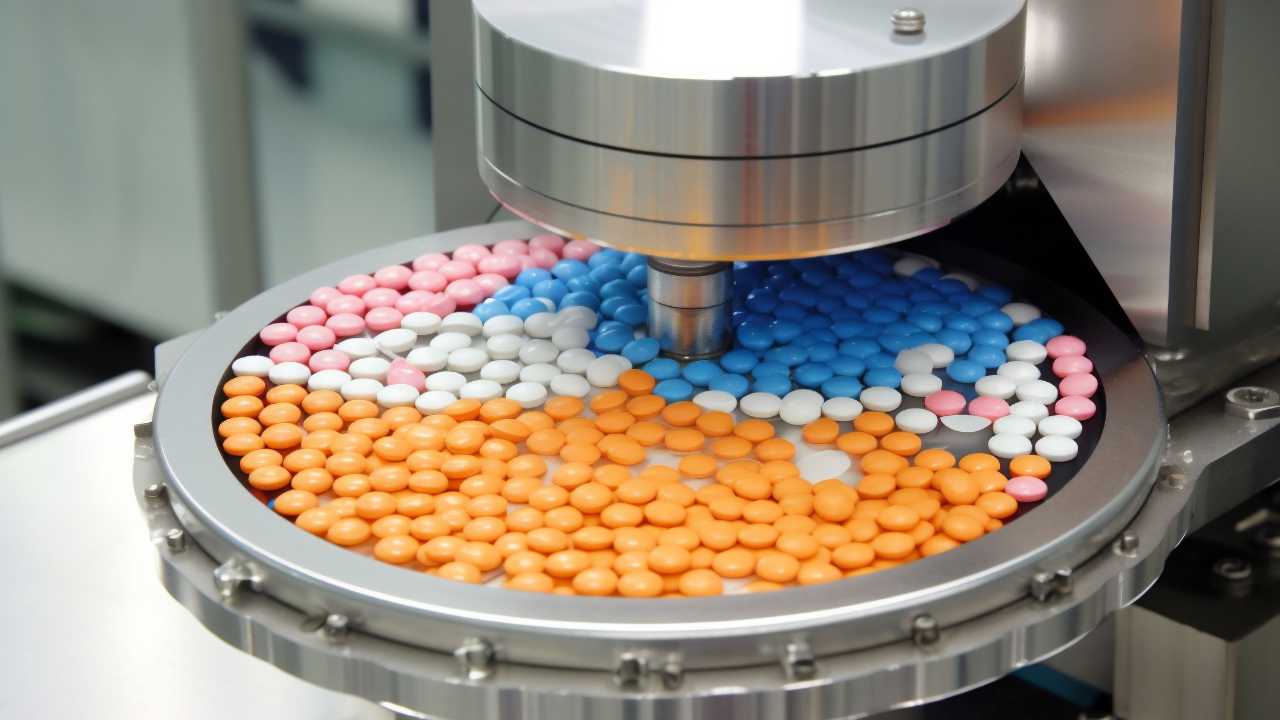
Pharmaceutical manufacturing is a complex journey. From the initial discovery of a potential drug to its eventual arrival in the hands of patients, the process involves numerous steps and careful considerations. One important milestone in this journey is scaling up manufacturing.
In simple terms, this means making more of the medicine to meet the needs of larger clinical trials and, eventually, for widespread distribution. Let’s understand the basics of pharmaceutical manufacturing and explore the essential factors to consider when scaling up production.
Understanding the Drug Development Timeline
Before we talk about scaling up, it’s important to understand where it fits in the drug development timeline. The journey begins with the discovery and formulation of a drug, where scientists combine the active drug with other ingredients to create a usable form. Next comes preclinical testing, where the drug’s safety and effectiveness are evaluated in animals.
If the drug passes these early tests, it moves into human clinical trials, divided into four phases. Phase I involves a small group of healthy volunteers testing the drug for safety and the right dose. Phase II expands to a larger group with the targeted disease, assessing effectiveness. Phase III involves an even larger group to confirm safety and effectiveness compared to existing treatments. Finally, Phase IV, after approval, may include additional studies for long-term safety and effectiveness.
Scaling up manufacturing usually happens during Phase III, after the drug has proven safe and effective in smaller groups. At this point, the drug is close to its final form that will reach the market.
What Does Scaling Up Mean?
Scaling up pharmaceutical manufacturing is like making a recipe for a larger party. Imagine you usually make a small batch of cookies at home. Scaling up means adjusting the recipe, ingredients, and tools to make a much larger batch for a big celebration. In the pharmaceutical world, this involves making adjustments to produce more of the drug while maintaining quality, safety, and consistency.
Here is what scaling up includes:
1. Adjusting Equipment and Vessels: Imagine you have a small blender at home for your smoothies. If you need to make more smoothies for a crowd, you might use a larger blender. In pharmaceutical manufacturing, this involves adjusting the size of equipment and vessels used in the production process.
2. Increasing Batches: If you usually make one batch of cookies, scaling up means making multiple batches to meet the demand. Similarly, in pharmaceuticals, you increase the number of batches produced.
3. Quality Control Measures: Just like you taste a small batch of cookies to ensure they are perfect before making more, in pharmaceuticals, rigorous quality control measures are implemented. This ensures each batch of the drug meets strict quality standards.
4. Optimizing the Process: Think of optimizing as finding the most efficient way to bake your cookies. In pharmaceuticals, optimizing the manufacturing process ensures it runs smoothly and efficiently.
5. Regulatory Guidelines: Imagine there are rules for how you can prepare food for a large event. Similarly, pharmaceutical manufacturing must follow strict regulatory guidelines set by authorities to ensure safety and quality.
Why Scaling Up is Important
Now let us understand why scaling up business is so important. There are three big reasons for this:
1. Patient Safety: Before a new drug can be sold, it goes through extensive testing in clinical trials involving many participants. Scaling up ensures the manufacturing process produces consistent, high-quality batches of the drug, keeping patients safe.
2. Regulatory Approval: To sell a new drug, it must meet strict quality standards set by agencies like the FDA. These standards apply not just to the final product but also to how it’s made. Scaling up while following guidelines ensures regulatory approval.
3. Commercial Success: Imagine you made the best cookies in town, but you could only bake a few at a time. Scaling up allows pharmaceutical companies to produce more efficiently and at lower costs, making the difference between profit and loss.
Tips for Successful Scale-Up
Scaling up isn’t a one-size-fits-all process; each drug is unique. However, here are some simple tips that apply to most cases:
1. Work with Experienced Partners: It’s like having a seasoned chef help you with your big cooking project. Experienced partners in Contract Development and Manufacturing Organizations (CDMOs) can assist in planning and executing the scale-up.
2. Plan for Regulatory Compliance: Think of this as making sure your cooking follows health and safety regulations. Plan for regulatory compliance early to avoid delays or issues later.
3. Establish Quality Control Measures: Just as you taste your food to check quality, establish robust quality control measures early on. This ensures the final product meets all regulatory requirements.
4. Pay Attention to Process Development: Consider this as fine-tuning your recipe. Developing and validating the manufacturing process is key. It includes defining process parameters, testing for efficacy, and following guidelines.
5. Understand Raw Material Impact: Different ingredients can affect your cookies. Similarly, raw materials can impact the manufacturing process. Understand how various raw materials affect production.
6. Be Prepared for Changes: Scaling up may require changes in your process. Plan for these changes to be quick and efficient. It’s like having a backup recipe if your first one doesn’t quite work.
7. Facility Design for Scalability: Ensure your cooking space is designed for growth. Partnering with a CDMO eliminates concerns about facility design, as they already have what’s needed for both small and large-scale manufacturing.
Challenges in Scaling Up Pharmaceutical Manufacturing
Scaling up pharmaceutical manufacturing presents significant challenges that require careful consideration and proactive measures. These challenges can impact various aspects of the production process and necessitate strategic planning for successful outcomes.
Ensuring Regulatory Compliance
One of the primary hurdles in scaling up is ensuring regulatory compliance. Navigating through the stringent requirements set by regulatory authorities, such as the FDA, demands early planning and collaboration with experienced partners. This involves adhering to guidelines to secure regulatory approval, an important step in the pharmaceutical manufacturing journey.
Minimizing Costs
Cost management is a critical aspect of scaling up pharmaceutical production. The process should be designed to minimize costs while maintaining efficiency. Efficient utilization of raw materials and optimizing production processes are essential components of a successful scale-up strategy. By carefully managing costs, pharmaceutical companies can enhance their financial viability during the expansion phase.
Maintaining Quality
As production scales up to larger batches, maintaining product quality becomes a complex challenge. Stringent quality control measures must be established and adhered to at every stage of the manufacturing process. Attention to detail is paramount to ensure that each batch meets the required quality standards. This focus on quality is vital to guarantee the safety and efficacy of the pharmaceutical product.
Remaining Flexible
Flexibility is key when scaling up pharmaceutical manufacturing, as unexpected challenges are bound to arise. Issues such as supply chain disruptions or equipment glitches can impact the production process. Being prepared with a contingency plan is essential to handle these unforeseen circumstances effectively. The ability to adapt to changes swiftly and efficiently is important for maintaining a smooth and uninterrupted manufacturing process.
Process of Scaling Up Pharmaceutical Manufacturing
The process of scaling up pharmaceutical manufacturing involves the following steps:
Batch Size Consideration:
In the initial phase of scaling up pharmaceutical manufacturing, careful consideration of batch size is paramount. This involves a careful approach to determining the batch size based on annual forecasts and projected launch quantities. Furthermore, it is important to align the batch size for the final product, Active Pharmaceutical Ingredient (API), and raw materials to ensure a cohesive and streamlined production process.
Raw Material Consistency:
Ensuring the consistency of raw materials adds a layer of complexity to the scaling-up process. This step involves not only obtaining materials from the same supplier but also minimizing variations in raw material grades. This meticulous approach aims to establish correlations and eliminate potential material interactions that could impact the quality and integrity of the pharmaceutical product.
Documentation and Data Analysis:
A comprehensive approach to documentation and data analysis is essential for successful scale-up. This involves charting the development progress and small-scale batches meticulously. Variables derived from product documentation are identified and analyzed. Additionally, a parallel chart is created for the proposed manufacturing process, ensuring a thorough understanding and alignment of every aspect.
Process Changes and Critical Steps:
As the scale increases, critical steps identified during small-scale manufacturing are rigorously challenged. This step involves a detailed reevaluation of other process steps that may be impacted at a larger scale. Addressing these critical steps ensures the scalability and integrity of the manufacturing process.
Data Comparisons and Insights:
A critical aspect of scaling up involves conducting rigorous data comparisons. This includes determining the comparability and scalability of each step in the process. The insights gained from this analysis are then utilized to make informed decisions, ensuring that the scaled-up process aligns seamlessly with the small-scale model.
Scale-Up Plan and Documentation:
Documenting the scale-up plan through a carefully crafted and approved protocol is a foundational step. This documentation outlines the intricate details of the scale-up process, providing a roadmap for implementation. Initially planning to manufacture 3-5 batches allows for a systematic and measured approach to scale-up.
Confirmation Batches:
The confirmation phase involves conducting batches using predefined target parameters. The evaluation of batch data at this stage is important for assessing comparability to small-scale lots. This thorough examination ensures that the scaled-up batches meet the established standards before progressing further.
Validation and Regulatory Approval:
Validation, a pivotal step in the scaling-up process, follows confirmation of batch comparability. This involves proceeding with a systematic validation process and seeking regulatory approval for the saleability of the batches. Regulatory compliance is of utmost importance to ensure adherence to industry standards and regulations.
Consideration for Manufacturing Loads:
For processes involving multiple manufacturing loads, each sublot is treated as an experiment. This involves meticulous data collection to ensure a comprehensive analysis of the impact of different manufacturing loads on the final product. This step adds an additional layer of assurance to the scalability and consistency of the manufacturing process.
Continued Monitoring and Adaptation:
The journey of scaling up pharmaceutical manufacturing doesn’t conclude with successful validation. Continuous monitoring of the manufacturing process is imperative. Being prepared to adapt swiftly and efficiently to unforeseen challenges during large-scale production ensures the ongoing success and sustainability of the scaled-up operation.
Conclusion
Scaling up pharmaceutical manufacturing is like growing a small garden into a thriving farm. It requires careful planning, attention to detail, and collaboration. Just as a delicious meal satisfies hungry guests, successful scale-up ensures that safe and effective medicines reach those who need them. So, whether you’re baking cookies or making medicine, remember, the key is to scale up wisely, ensuring quality and safety every step of the way.