We offer formulation development of high-quality nasal spray dosage forms. Hycon specializes in developing stable, viable drug formulations and ensuring optimal shelf life for delivery devices.
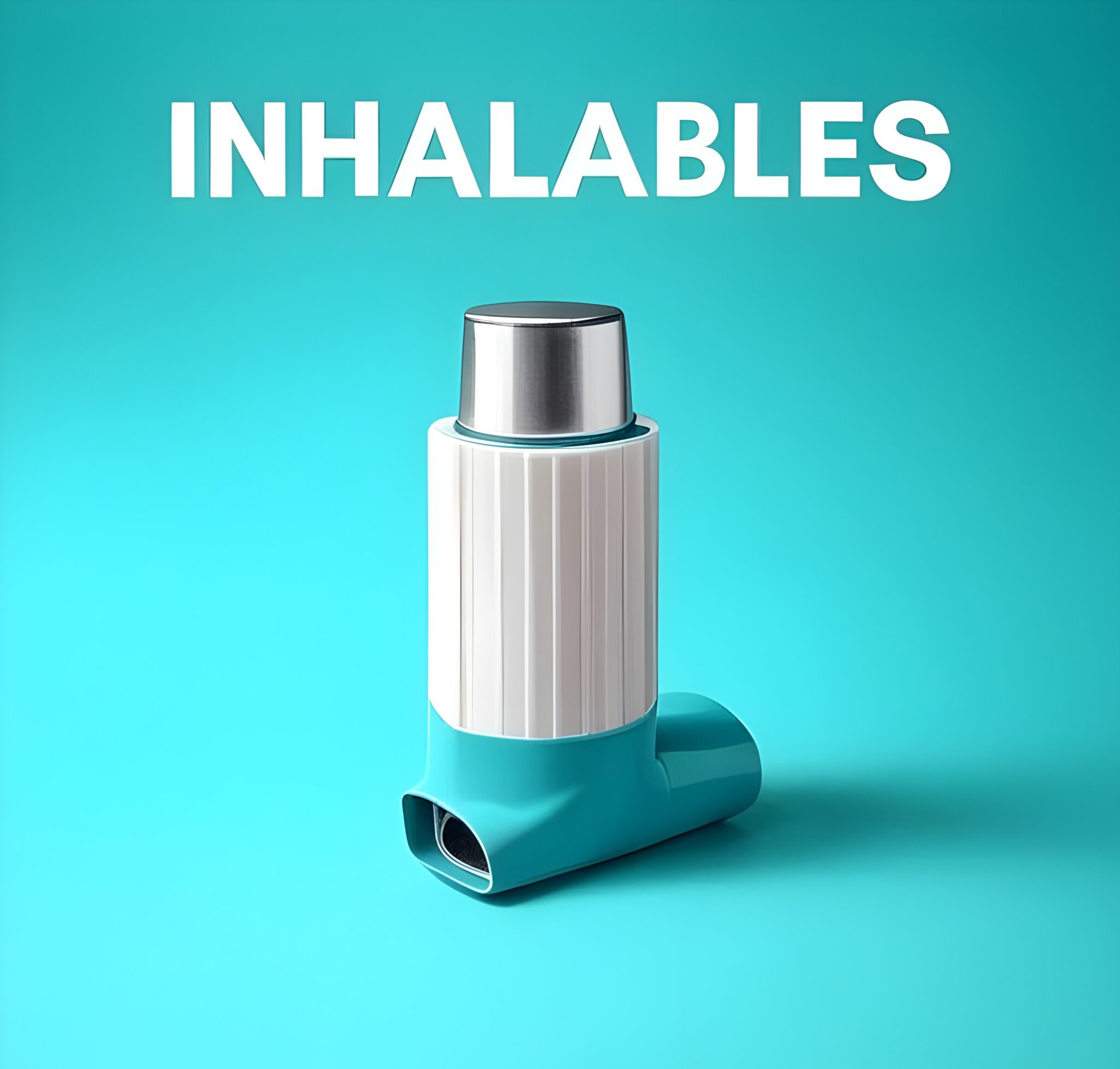
Formulation Development
Our formulation scientists utilize advanced techniques such as particle size reduction, spray drying, and super critical fluid technology to develop inhalable formulations with optimal aerodynamic properties. We also have expertise in the formulation of suspension, solution, and dry powder inhalables.
Analytical Development
Our analytical development services include physicochemical characterization of the API, in-vitro bioequivalence studies, and extractables and leachables studies. We use state-of-the-art analytical instruments such as Next Generation Impactor (NGI), High-Performance Liquid Chromatography (HPLC), and Mass Spectrometry (MS) for these analyses.
In-vitro Testing
In-vitro testing techniques such as cascade impaction are used to assess the aerodynamic properties of the inhalable particles, which can provide valuable information on the lung deposition behavior of the product.
Human Factors Engineering
Human factors engineering is applied to the design of the inhalation device to ensure ease of use and patient compliance. This includes considerations for the actuation force, inhalation flow rate, and ergonomics of the device.
I hope these additional details provide a more comprehensive overview of the challenges and techniques in the development of inhalables. Please feel free to reach out if you need more information.
Process Development for Inhalables and Nasal Products
Our process development team, specializing in inhalables and nasal products, utilizes Quality by Design (QbD) principles to optimize the manufacturing process. This includes:
Design of Experiments (DoE)
We conduct DoE to understand the impact of process parameters on the product quality attributes. For inhalables and nasal products, this could include parameters such as blending time, spray drying conditions, or filling speed, which can significantly affect the aerodynamic properties of the particles and the performance of the product.
Process Analytical Technology (PAT) Tools
We use PAT tools for real-time monitoring and control of the process. For instance, we may use in-line particle size analyzers during the milling process to ensure the particle size distribution is within the desired range for inhalables and nasal products.
Risk Assessment
We conduct risk assessment to identify and control potential risks in the manufacturing process that could affect the quality of the inhalables and nasal products. This could include risks associated with cross-contamination, equipment failure, or variability in raw material quality.
Process Optimization and Scale-up
We optimize the process to ensure it is robust, reproducible, and scalable. For inhalables and nasal products, this involves careful scale-up of the process to maintain the critical quality attributes such as particle size distribution, dose uniformity, and product stability.
Through these strategies, we ensure the development of high-quality, safe, and effective inhalable and nasal products. Our goal is to deliver a process that is not only efficient and reliable, but also ready for validation and commercial manufacturing.
Manufacturing Capabilities for Inhalables and Nasal Products
Dedicated Manufacturing Suites
We have dedicated manufacturing suites specifically designed for the production of inhalable and nasal products. These suites are equipped with air handling units to maintain the required temperature, humidity, and particulate levels, ensuring the quality and safety of the products.
Pressurized Metered-Dose Inhalers (pMDIs)
Our facilities are equipped with high-speed filling lines for pMDIs. These lines are capable of handling both solution and suspension formulations. They include features such as weight checking, leak detection, and crimping to ensure the quality and integrity of the pMDIs.
Dry Powder Inhalers (DPIs)
We have blending and filling equipment for DPIs. The blending equipment ensures a uniform distribution of the API in the carrier particles. The filling equipment is capable of filling both unit-dose and multi-dose DPIs with high accuracy and precision.
Clinical Trial Manufacturing
We follow ICH Q8, Q9, and Q10 guidelines for the manufacturing of clinical trial batches. We also provide ICH-compliant stability studies and packaging and labeling services for clinical trial materials.
Commercial Manufacturing
Our commercial manufacturing capabilities include batch and continuous manufacturing of inhalable products. We have automated packaging lines for canister insertion, actuator placement, and pouching of inhalable products.
Quality Assurance
Our quality assurance team ensures compliance with all relevant regulatory guidelines including US FDA, EMA, and ICH guidelines. We have a robust Quality Management System (QMS) in place, which includes procedures for change control, deviation management, CAPA, and risk management.
Challenges in Inhalables Development
API Characteristics
The physicochemical properties of the API, such as particle size, solubility, and stability, can pose significant challenges in the formulation of inhalable products. For instance, APIs with poor aqueous solubility may require the use of solubilizing agents or alternative formulation strategies.
Formulation Stability
Ensuring the stability of the formulation over its shelf-life is a major challenge. This includes both physical stability (e.g., prevention of agglomeration) and chemical stability (e.g., prevention of degradation).
Dose Uniformity
Achieving uniform dose delivery with each actuation is critical for the safety and efficacy of inhalable products. This can be particularly challenging for suspension-based pMDIs.
Patient Compliance
Inhalable products require correct inhalation technique for effective drug delivery. Ensuring ease of use and patient compliance can be a significant challenge.
Related Services
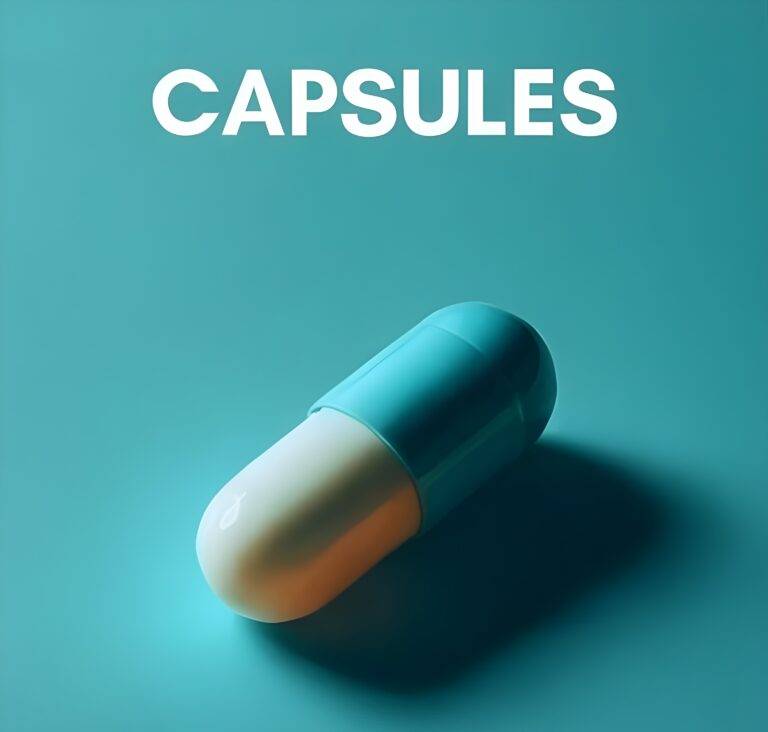
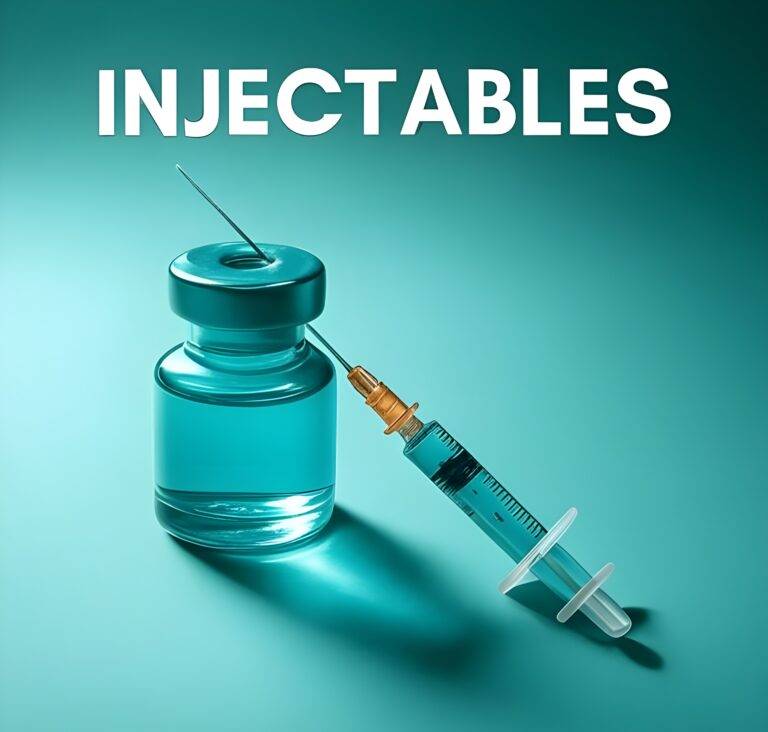
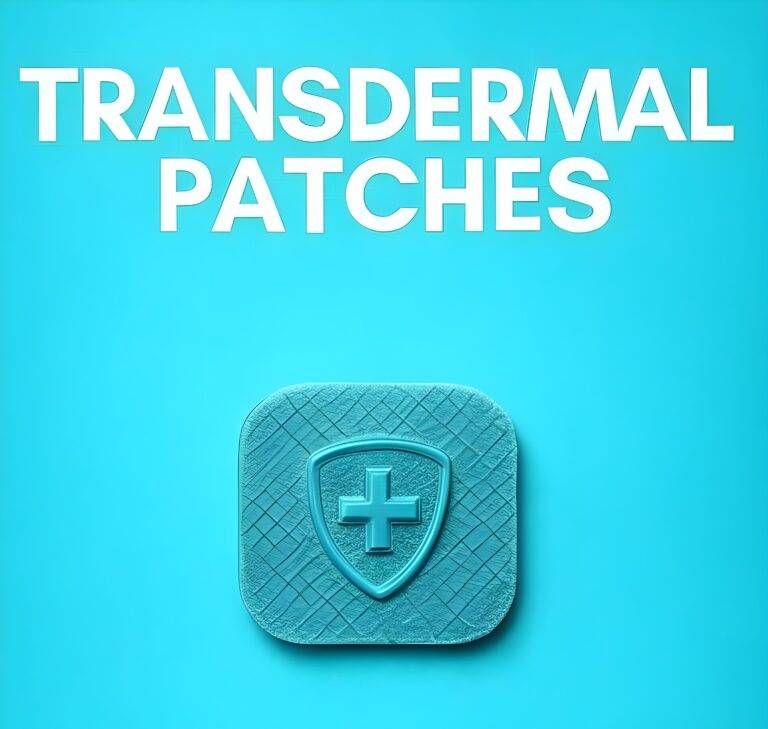
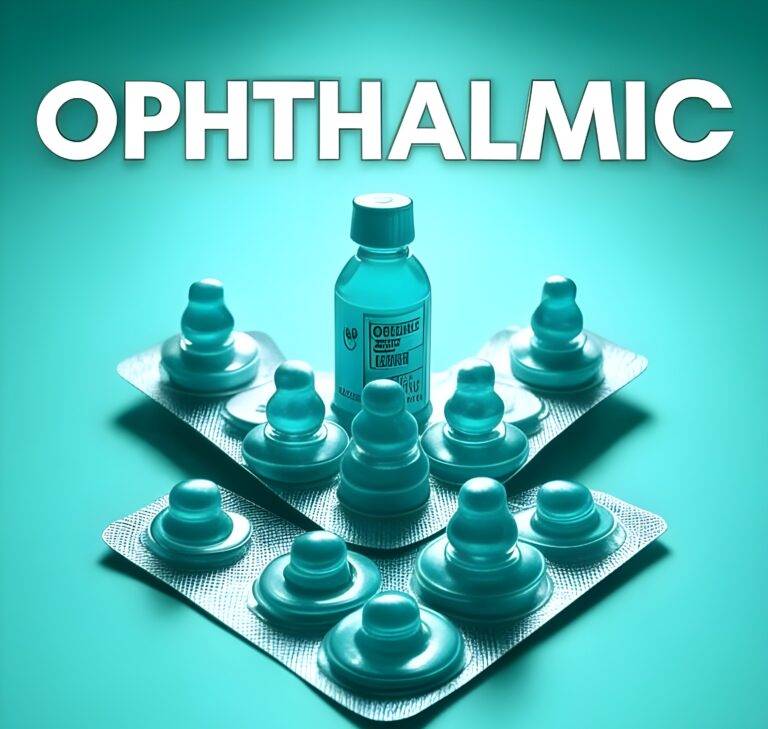
FAQs
Here are some frequently asked questions about Inhalables / Nasal.
Hycon provides comprehensive contract development and manufacturing services for inhalable and nasal drug products. This includes formulation development, clinical manufacturing, and supply of high-quality nasal spray dosage forms, as well as solutions for nebulization.
Yes, We have unrivaled expertise in formulating complex dosage forms to increase bioavailability or achieve controlled release for challenging APIs, including nasal solutions and suspensions.
We offer a full range of services from preclinical development to commercial manufacturing, encompassing small, pilot, full-scale, and adaptive manufacturing solutions across all clinical trial phases.
Hycon utilizes cutting-edge technologies and innovative techniques dedicated to enhancing the solubility and bioavailability of orally inhaled and nasal drug products, ensuring effective solutions for partners.
Hycon ensures compliance with stringent industry standards, guaranteeing product integrity and timely market entry with products that meet or exceed the highest quality benchmarks.
With extensive experience in small molecule oral dosage development and multi-modality manufacturing, Hycon is a preferred partner for its ability to optimize product development, launch, and full life-cycle supply.
Absolutely, Hycon offers customized solutions with a variety of dosage forms to increase efficacy, bioavailability, adherence, and safety for inhalable and nasal drug products.
Hycon boasts state-of-the-art GMP facilities dedicated to the clinical manufacturing of a diverse range of oral products, including inhalable and nasal drugs.
Hycon has over 300+ state-of-the-art equipment and facilities that can seamlessly adapt to evolving needs from early development stages to large-scale production.