Pharmaceutical liquids are pourable formulations that contain a mixture of active drug components and excipients dissolved or suspended in a suitable solvent or mixture of solvents. These formulations are designed to provide maximum therapeutic response, especially for populations with difficulty swallowing solid dosage forms, and to produce rapid therapeutic effects.
Characteristics of Pharmaceutical Liquids
- Composition: Pharmaceutical liquids consist of active drugs and excipients such as emulsifying, dispersing, solubilizing, stabilizing, suspending, wetting, thickening agents, preservatives, sweetening agents, flavoring agents, and coloring agents..
- Types: They can be supplied as ready-to-use liquids or powders for reconstitution. They are administered by various routes including oral, parenteral (injectable), inhalation, ophthalmic, otic, nasal, and topical.
- Monophasic and Biphasic Forms: Liquid dosage forms are broadly classified into monophasic (single-phase) and biphasic (two-phase) systems. Monophasic forms include solutions, syrups, and elixirs, while biphasic forms include suspensions and emulsions.
Advantages of Pharmaceutical Liquids
Liquids offer a fluid approach, addressing challenges related to patient compliance, formulation flexibility, bioavailability, and development speed. Whether it’s syrups, injectables, or oral solutions, we have you covered. Here are some detailed insights into the advantages and challenges of liquid formulations:
- Patient Compliance: Liquid formulations are easier to swallow, making them ideal for pediatric and geriatric patients who may have difficulty with tablets or capsules. The pleasant taste and ease of administration improve patient adherence to medication regimens.
- Formulation Flexibility: Liquids allow for a wide range of formulations, including solutions, suspensions, emulsions, and syrups. This flexibility enables the incorporation of various active pharmaceutical ingredients (APIs) and excipients to achieve desired therapeutic effects.
- Bioavailability: Liquid formulations often provide better bioavailability compared to solid dosage forms. The drug is already in a dissolved state, which facilitates faster absorption and onset of action.
- Development Speed: Liquid formulations can be developed and scaled up more quickly than solid dosage forms. This is particularly advantageous in situations where rapid product development is essential.
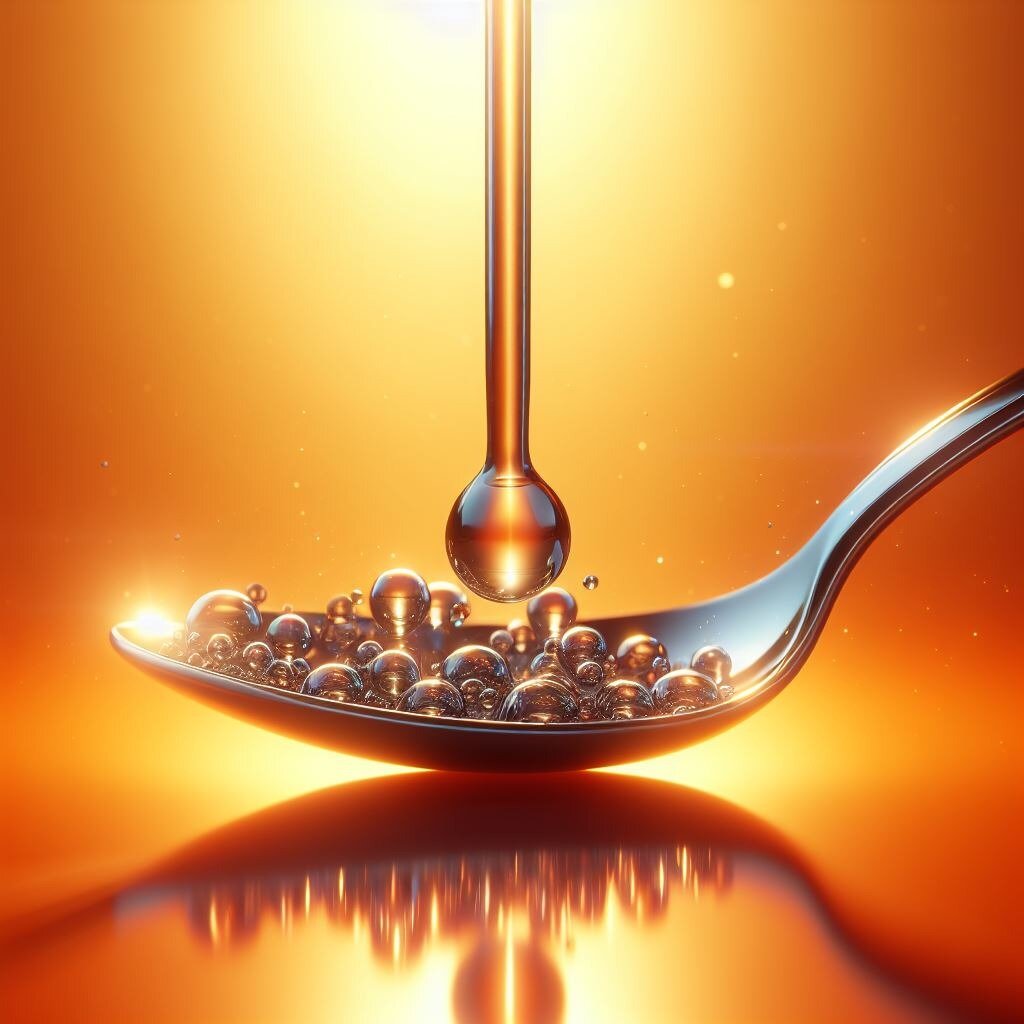
Our Approach
- Integrated Services: Our fully integrated pharmaceutical development and liquid dosage manufacturing services cover oral solutions and suspensions, including pediatric liquid dose forms.
- Seamless Transition: With development facilities co-located within our commercial manufacturing operations, we seamlessly transition from pre-formulation and formulation development to clinical studies and commercial production.
- Expertise: Our liquids expertise is backed by in-house quality and microbiology labs, robust quality systems, and a team of highly skilled technicians.
- Global Reach: We currently supply liquid dosage forms commercially to the US and have the capacity to do so in Canada, Europe, and Asia.
Manufacturing Capabilities
Our manufacturing capabilities span a wide range of advanced technologies to ensure the highest quality and compliance with regulatory standards:
Batch Sizes
Liquid cGMP: Our facility is equipped to handle liquid formulations with batch sizes ranging from 10 liters to 1,000 liters. This flexibility allows us to cater to both small-scale clinical trials and large-scale commercial production. The ability to scale up or down ensures that we can meet the varying demands of different stages of drug development.
Suspension cGMP: Similarly, we can manage suspension formulations with batch sizes also ranging from 10 liters to 1,000 liters. This range ensures that we can accommodate various stages of product development and production needs, from initial formulation trials to full-scale manufacturing.
Segregated Suites
We maintain segregated suites to ensure product integrity and compliance. These suites are designed to prevent cross-contamination and ensure that each product is manufactured in a controlled environment. This is particularly important for products that require stringent isolation due to their potency or sensitivity.
Compartmentalized Environment and XP Liquid Compounding
Our compartmentalized environment and XP liquid compounding facilities provide precise control over the manufacturing processes. This setup allows for the accurate mixing and compounding of liquid formulations, ensuring consistency and quality. The compartmentalized design also helps in maintaining a clean and controlled environment, which is crucial for the production of high-quality pharmaceuticals.
Controlled Substances (CI – CV)
We have the expertise to handle controlled substances ranging from Schedule I to Schedule V. Our facility is equipped with secure storage and handling protocols to ensure compliance with regulatory requirements and prevent diversion or misuse. This includes rigorous documentation and monitoring systems to track the movement and usage of controlled substances within the facility.
Vessel Options
We offer an extensive range of vessel types for various formulations. Our vessels are designed to meet the specific needs of different pharmaceutical processes, including mixing, blending, and storage. Options include:
- Jacketed vessels: Vacuum-rated, steam-heated, and water-cooled for precise temperature control. These vessels are essential for processes that require specific temperature conditions to maintain the stability and efficacy of the product.
- Agitated vessels: Equipped with mixers and agitators for uniform mixing. These vessels ensure that all components are thoroughly mixed, which is critical for the consistency and quality of the final product.
- Pressure vessels: Designed to withstand high pressures for certain formulations. These vessels are used in processes that require pressurization to achieve the desired chemical reactions or product characteristics.
Filtration and Mixing Options
Our facility provides customized filtration and mixing solutions to achieve optimal results. We utilize various filtration techniques, including sterile filtration, to ensure the purity and sterility of our products. Our mixing equipment is designed to handle different types of mixtures, from simple solutions to complex suspensions. This versatility allows us to tailor our processes to the specific needs of each product.
Vacuum-Rated, Steam-Heated, and Water-Cooled Jacketed Vessels
We use vacuum-rated, steam-heated, and water-cooled jacketed vessels to provide versatile equipment options for different manufacturing processes. These vessels allow for precise temperature control, which is crucial for maintaining the stability and efficacy of pharmaceutical products. The ability to control temperature accurately helps in preventing degradation and ensuring the quality of the final product.
Nitrogen/Inert Gas Blanketing
To ensure stability and safety, we employ nitrogen and inert gas blanketing. This technique involves replacing the atmosphere in storage tanks and reaction vessels with an inert gas, such as nitrogen, to prevent oxidation and degradation of sensitive compounds. Nitrogen blanketing is particularly important for products that are sensitive to oxygen and moisture, as it helps in maintaining their stability and extending their shelf life.
HEPA Air Filtration
Our facility is equipped with HEPA air filtration systems to maintain clean environments. HEPA filters remove particles as small as 0.3 microns, including bacteria, viruses, and dust, ensuring that our manufacturing areas meet the highest standards of cleanliness and sterility. This is essential for preventing contamination and ensuring the safety and efficacy of our products.
Light-Sensitive Materials
For formulations that are sensitive to light, we offer specialized facility lighting options. This includes the use of amber lighting and protective packaging to prevent photodegradation and ensure the stability of light-sensitive products. Light-sensitive products are protected from exposure to harmful wavelengths of light, which can cause degradation and reduce their efficacy.
By leveraging these advanced technologies and capabilities, we are able to deliver high-quality pharmaceutical products that meet stringent regulatory requirements and address the diverse needs of our clients.
Liquid Dosage Formulations
We specialize in both monophasic and biphasic formulations, each offering unique advantages for different pharmaceutical applications.
- Monophasic Formulations: These are homogeneous liquid preparations where the active pharmaceutical ingredient (API) is completely dissolved in the vehicle. Examples include solutions, syrups, elixirs, and linctuses. Monophasic formulations are known for their ease of administration, rapid onset of action, and high bioavailability. They are particularly suitable for drugs that are highly soluble in water and require immediate release.
- Biphasic Formulations: These consist of two phases, typically a solid phase dispersed in a liquid phase. Examples include suspensions and emulsions. Biphasic formulations are beneficial for APIs that are poorly soluble in water, providing controlled release and improved stability. They are ideal for drugs that require sustained or controlled release to maintain therapeutic levels over an extended period.
Oral Liquid Dosage
Our tailored solutions for oral liquid dosage forms focus on enhancing taste-masking, bioavailability, and patient compliance. Key aspects include:
- Taste-Masking: Utilizing flavoring agents, sweeteners, and encapsulation techniques to mask the unpleasant taste of APIs, making the medication more palatable, especially for pediatric and geriatric patients. Techniques such as microencapsulation and the use of ion exchange resins are commonly employed to achieve effective taste-masking.
- Bioavailability Enhancement: Implementing solubility enhancement techniques such as micronization, solid dispersions, and the use of surfactants to improve the bioavailability of poorly soluble drugs. Techniques like self-emulsifying drug delivery systems (SEDDS) and nanoemulsions are also used to enhance the absorption of lipophilic drugs.
- Patient Compliance: Designing formulations that are easy to administer, with accurate dosing and pleasant taste, to improve patient adherence to medication regimens. This includes the development of unit-dose packaging and the use of child-resistant and senior-friendly packaging solutions.
Aqueous and Solvent-Based Systems
We offer versatile options for drug delivery through both aqueous and solvent-based systems:
- Aqueous Systems: These include water-based solutions and suspensions, which are generally preferred for their safety, compatibility, and ease of administration. Aqueous systems are ideal for hydrophilic drugs and are commonly used in pediatric and geriatric formulations due to their ease of swallowing.
- Solvent-Based Systems: These involve the use of organic solvents to dissolve APIs that are poorly soluble in water. Examples include ethanol, propylene glycol, and glycerin-based formulations. Solvent-based systems can enhance the solubility and stability of certain drugs, making them suitable for lipophilic drugs and those requiring rapid absorption.
High-Pressure and High-Shear Homogenization
Our expertise in high-pressure and high-shear homogenization allows us to achieve efficient particle size reduction, which is crucial for the stability and bioavailability of pharmaceutical formulations:
- High-Pressure Homogenization: This technique involves passing the liquid through a narrow gap at high pressure, resulting in the reduction of particle size and the formation of stable emulsions or suspensions. It is widely used for the production of nanoemulsions, liposomes, and other colloidal systems. High-pressure homogenization is particularly effective for creating uniform particle sizes and enhancing the stability of emulsions.
- High-Shear Homogenization: This method uses mechanical shear forces to break down particles and droplets, ensuring uniform distribution and stability of the formulation. It is particularly useful for the preparation of suspensions and emulsions. High-shear homogenization is often employed in the initial stages of formulation development to achieve the desired particle size distribution.
Oral Suspensions
Our oral suspensions are designed for controlled release and stability, providing an effective alternative for patients who have difficulty swallowing solid dosage forms:
- Controlled Release: By incorporating appropriate suspending agents and stabilizers, we ensure that the active ingredients are uniformly dispersed and released at a controlled rate. This is achieved through the use of polymers such as hydroxypropyl methylcellulose (HPMC) and xanthan gum, which help maintain the suspension’s stability and control the release of the API.
- Stability: Our formulations are optimized to prevent sedimentation and aggregation, maintaining the stability and efficacy of the suspension over its shelf life. Techniques such as particle size reduction, the use of wetting agents, and the incorporation of preservatives are employed to enhance the stability of oral suspensions.
Product Heating and Cooling
Precise temperature control is essential in pharmaceutical manufacturing to ensure product quality and stability:
- Heating: Controlled heating processes are used to dissolve APIs, sterilize formulations, and facilitate chemical reactions. It is crucial to avoid overheating, which can degrade sensitive ingredients. Techniques such as jacketed vessels and heat exchangers are commonly used to achieve precise temperature control during the heating process.
- Cooling: Rapid cooling is employed to stabilize formulations, prevent crystallization, and enhance the solubility of certain drugs. Proper cooling techniques are essential to maintain the integrity and efficacy of the final product. Cooling methods such as cryogenic cooling and the use of cooling tunnels are utilized to achieve the desired temperature control.
Packaging Capabilities
Liquid Packaging Lines
Our liquid packaging lines are designed to accommodate a wide variety of formulations, ensuring flexibility and precision in packaging. We utilize advanced technologies and adhere to stringent quality standards to deliver reliable and consistent products.
Glass or Plastic Bottles
We offer packaging solutions in both glass and plastic bottles, with sizes ranging from 10 mL to 4 liters. Each material has its own advantages and is selected based on the specific requirements of the formulation:
- Glass Bottles: Glass is an inert material, making it ideal for packaging sensitive formulations that may react with other materials. It provides excellent barrier properties, protecting the contents from moisture, oxygen, and other environmental factors. Glass bottles can also be amber-colored to protect light-sensitive formulations from photodegradation.
- Plastic Bottles: Plastic bottles are lightweight, durable, and shatterproof, making them a practical choice for many formulations. They can be made from various types of plastics, such as polyethylene terephthalate (PET), high-density polyethylene (HDPE), and low-density polyethylene (LDPE), each offering different levels of rigidity, flexibility, and chemical resistance. Plastic bottles are also available in different colors to protect light-sensitive products.
Benefits of Liquid Dosage Forms
Enhancing Patient Compliance
Patient Acceptability: Liquid formulations, such as syrups, suspensions, and solutions, offer better palatability and ease of administration, especially for children and the elderly. These formulations can be flavored and sweetened to mask the unpleasant taste of certain drugs, making them more acceptable to patients. This is particularly important for pediatric and geriatric populations who may have difficulty swallowing tablets or capsules.
Improved Adherence: Enhanced patient acceptability leads to better medication adherence. When patients find their medication easier to take, they are more likely to follow their prescribed treatment regimen, ultimately contributing to improved treatment outcomes. This is crucial for chronic conditions where long-term medication adherence is necessary for effective management.
Versatility and Flexibility
Formulation Flexibility: Unlike solid doses, liquid formulations provide greater flexibility. Adjusting dosage or delivering specific drug combinations is easier with liquids. This flexibility is particularly beneficial for drugs that require precise dosing adjustments. For example, in pediatric medicine, where age- and weight-based dosage adjustments are common, liquid formulations allow for easy modification of doses to suit individual patient requirements.
Critical in Pediatrics: Liquid Contract Development and Manufacturing Organizations (CDMOs) excel in tailoring formulations to meet specific patient needs. This is crucial in pediatric medicine, where age- and weight-based dosage adjustments are common. Liquid formulations allow for easy modification of doses to suit individual patient requirements. This flexibility ensures that children receive the correct dose for their age and weight, which is essential for safety and efficacy.
Optimizing Bioavailability
Enhanced Bioavailability: Liquid medications often exhibit better bioavailability compared to solid counterparts. This is because the drug is already in a dissolved state, which facilitates quicker absorption into the bloodstream. Improved bioavailability ensures that a higher percentage of the drug reaches the systemic circulation, leading to more consistent therapeutic outcomes.
Quicker Onset of Action: Rapid absorption of liquid drugs leads to a faster onset of action, which is vital in acute treatment scenarios. For instance, in emergency situations where immediate drug action is required, liquid formulations can provide quicker relief. This is particularly important for conditions such as pain management, where rapid onset of action can significantly improve patient comfort.
Speed to Market and Efficiency
Efficient Development: Liquid formulation and production processes are often faster and more straightforward than complex solid dose manufacturing. This efficiency can reduce the time and cost associated with drug development. The simplicity of liquid formulations allows for quicker scale-up and manufacturing, enabling pharmaceutical companies to bring new products to market more rapidly.
Accelerated Timelines: Liquid dosage forms enable pharmaceutical companies to respond swiftly to market demands and regulatory requirements. The ability to quickly develop and produce liquid formulations can be a significant advantage in the competitive pharmaceutical industry. This agility allows companies to meet urgent medical needs and capitalize on market opportunities.
Additional Benefits
Better for Patients with Swallowing Difficulties: Liquid dosage forms are particularly suitable for patients who have difficulty swallowing tablets or capsules, such as pediatric or geriatric patients. This ensures that these patients can receive their medication without discomfort or risk of choking.
Higher Flexibility in Dosing: The dose of the drug substance can be easily and conveniently adjusted by measuring a different volume, providing higher flexibility in dosing compared to solid dosage forms. This is especially useful in situations where precise dosing is critical, such as in pediatric or geriatric populations.
Effective for Certain Types of Products: Products like adsorbents and antacids are more effective in liquid dosage form. Additionally, liquid dosage forms are expected for certain types of products like cough medications. The liquid form allows for better coating of the throat and faster relief of symptoms.
Improved Drug Stability: Liquid formulations can enhance the stability of certain drugs that are hygroscopic or deliquescent and not suitably dispensed in solid dosage forms. This ensures that the drug remains effective throughout its shelf life.
Related Services
FAQs
Here are some frequently asked questions about Liquids.
Hycon provides comprehensive liquid formulation services, including pre-formulation, formulation development, stability studies, and scale-up. We specialize in solutions, suspensions, emulsions, and other liquid dosage forms, ensuring high bioavailability and patient compliance.
With our state-of-the-art equipment and experienced team, we can cut up to 20 weeks off your early and late phase timelines. Our streamlined processes and proactive risk mitigation strategies ensure faster development without compromising quality.
Our liquid formulations are designed for maximum efficacy and safety. We employ advanced technologies and innovative approaches to enhance bioavailability and ensure controlled release, even for the most challenging APIs.
Absolutely. We have the scalability to adapt to your evolving needs, from early development stages to large-scale production. Our facilities are equipped to handle all batch sizes, ensuring a reliable supply for global markets.
Quality assurance is at the core of what we do. We guarantee product integrity and timely market entry by adhering to stringent industry standards and employing comprehensive analytical testing and method development for quality and validation.
Our management team averages over 30 years of industry knowledge. This wealth of experience ensures that your liquid formulation projects are guided by proven professionals who are well-versed in the latest pharmaceutical development techniques.
We have dedicated scientists, engineers, and quality personnel who specialize in pharmaceutical technology transfers. This ensures a seamless transition of your liquid formulation projects from one stage to the next, maintaining consistency and quality throughout.
We offer strategic regulatory planning and quality assurance to ensure global compliance. Our team supports product lifecycle management, streamlining approvals to facilitate a smooth path to market for your liquid formulations.
Yes, we offer comprehensive, end-to-end capabilities that support the entire pharmaceutical development and manufacturing process for liquid formulations. This includes everything from preclinical development to commercial production, providing you with a one-stop-shop solution for all your CDMO needs.