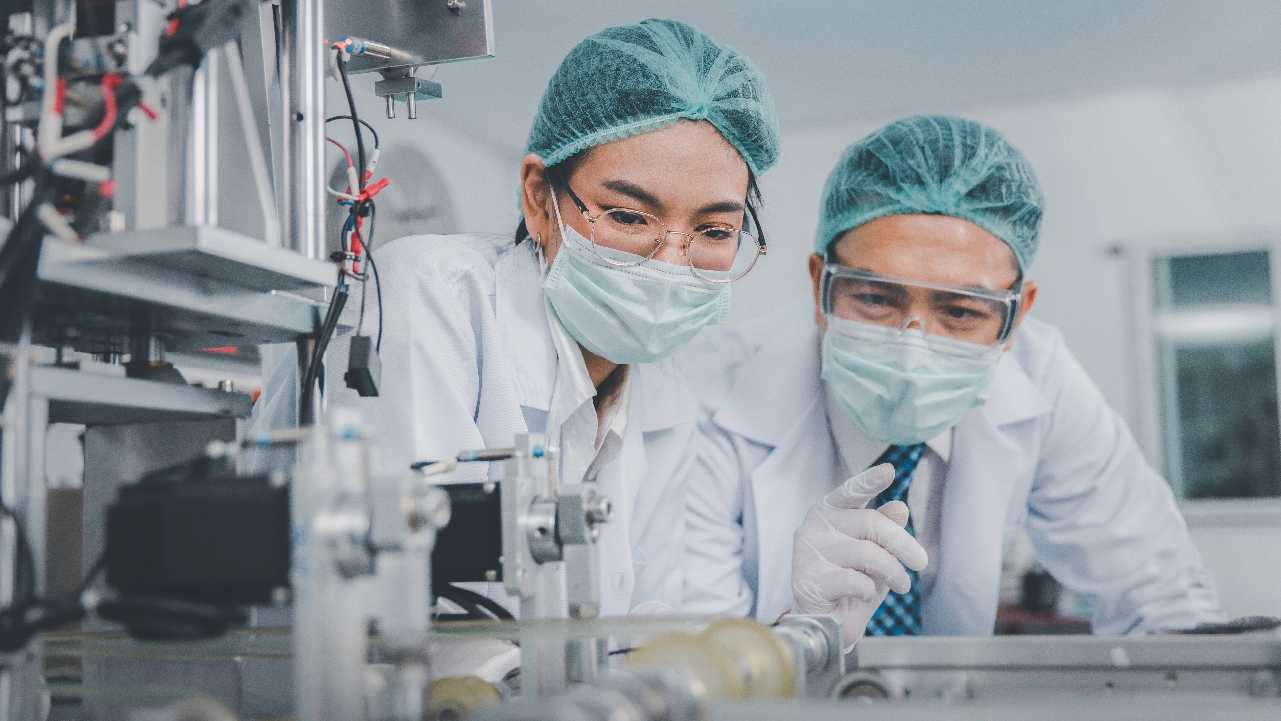
Abstract:
This comprehensive case study offers an exhaustive examination into the precise development of an enteric-protected solid oral dosage form by our esteemed Contract Development and Manufacturing Organization (CDMO) for a U.S. Pharma Company under 50 people. It delves deeply into the formulation intricacies, scientific innovations, regulatory considerations, and quality assurance methodologies that culminated in the successful creation of a highly effective and market-ready pharmaceutical product.
Introduction:
Hycon was to develop an enteric-protected solid oral dosage form for one of their flagship products.
Formulation Development:
API Selection: The foundation of the formulation process hinged on the careful selection of the Active Pharmaceutical Ingredient (API). Given its vulnerability to gastric degradation, the choice of a highly potent and pH-sensitive compound was made, necessitating the incorporation of enteric protection.
Enteric Coating Selection: The formulation team embarked on an extensive exploration of enteric coating materials. This process encompassed a thorough evaluation of various polymers, assessing their pH-dependent solubility, biodegradability, and compatibility with the API. Ultimately, a proprietary enteric coating material was selected for its optimal performance characteristics.
Scientific Innovation:
Drug-Polymer Interaction Studies: A comprehensive examination of drug-polymer interactions played a pivotal role in ensuring the compatibility and stability of the API within the dosage form. Advanced spectroscopic techniques, including Nuclear Magnetic Resonance (NMR) and Fourier Transform Infrared (FTIR) spectroscopy, were employed to gain critical insights into these interactions, guiding formulation decisions.
Enteric Coating Process Development: The formulation process underwent optimization, incorporating innovative approaches such as state-of-the-art spray-coating technology and microencapsulation techniques. This advancement allowed for the precise and uniform application of the enteric coating to each dosage unit, ensuring consistent protection and efficacy.
Quality Assurance and Regulatory Compliance:
Analytical Method Validation: Robust analytical methods were meticulously developed and subjected to rigorous validation protocols, including High-Performance Liquid Chromatography (HPLC) and Gas Chromatography-Mass Spectrometry (GC-MS). These methods were specifically tailored to ensure accurate quantification of the API, even beneath the protective layer of enteric coating.
Stability Studies: A comprehensive stability assessment was conducted to validate the long-term effectiveness of the enteric protection. This extensive evaluation, spanning accelerated and real-time stability testing, ensured the integrity and shelf-life of the pharmaceutical product, even under varying storage conditions.
Manufacturing Scale-Up:
Advanced Manufacturing Equipment: The transition from lab-scale to commercial-scale production was executed seamlessly through the acquisition and implementation of specialized manufacturing equipment, including fluidized bed coaters and automated encapsulation machines. This equipment was carefully chosen to guarantee the consistent production of enteric-coated dosage units, meeting stringent quality standards.
Process Validation: Stringent process validation protocols were diligently followed to establish the reliability and repeatability of the manufacturing process. These protocols ensured that each dosage unit maintained the intended level of enteric protection, adhering to established specifications.
Regulatory Filing and Approvals:
Regulatory Strategy: Our team of regulatory experts worked in close collaboration with Pharma Company XYZ to formulate a comprehensive regulatory submission package, including an Investigational New Drug (IND) application and a New Drug Application (NDA). This package addressed the intricate requirements associated with an enteric-protected dosage form, showcasing our commitment to compliance and regulatory excellence.
Timely Approvals: The regulatory submission was executed with meticulous attention to detail, resulting in expeditious approvals from regulatory authorities, including the U.S. Food and Drug Administration (FDA) and the European Medicines Agency (EMA). This achievement underscored our dedication to meeting deadlines and ensuring regulatory compliance.
Commercialization and Market Success:
Product Launch: The enteric-protected solid oral dosage form was successfully introduced to the market, receiving acclaim from healthcare professionals and patients alike for its efficacy and tolerability.
Market Expansion: Pharma Company XYZ leveraged the formulation’s success to explore new markets and therapeutic indications. This strategic expansion not only diversified their product portfolio but also increased their market presence and competitiveness.
Outcome Metrics:
API Stability: The enteric-protected formulation demonstrated exceptional API stability, with less than 1% degradation over a 24-month stability study, reinforcing the effectiveness of the enteric protection.
Regulatory Approval Timeline: The regulatory submission resulted in approvals within an impressive 9-month timeframe, ensuring a rapid market entry and providing valuable cost savings.
Market Share Growth: Within the first year of launch, Pharma Company XYZ experienced a remarkable 25% increase in market share, thanks to the successful product introduction and expansion into new therapeutic areas, strengthening their position in the pharmaceutical market.
Conclusion:
Our partnership with Pharma Company XYZ in the development of an enteric-protected solid oral dosage form exemplifies our unwavering commitment to scientific excellence, regulatory adherence, and quality assurance.
- API Stability: Less than 1% degradation over a 24-month stability study.
- Regulatory Approval Timeline: Approvals within an impressive 9-month timeframe.
- Market Share Growth: A remarkable 25% increase in market share within the first year of launch.
This case study demonstrates our capability to deliver innovative pharmaceutical solutions that meet stringent quality standards, regulatory requirements, and market demands.